压缩机排气管检测
压缩机生产线上的铜管通常容易发生微小形变,严重影响压缩机装配质量,需要在装配胶塞前对其进行检测。非夕的压缩机排气管检测方案利用自适应机器人及强通用性的工装,依靠仿人化的力控能力,替代传统人工矫管工序高效完成排气管检测。
案例介绍
客户:某知名压缩机生产商
背景:在为压缩机排气管装配胶塞前,需要对其用高精度矫管针做插检动作,有问题的排气管将会出现针无法插进或插不到位的情况,由此检测排气管口是否有变形、缺陷。
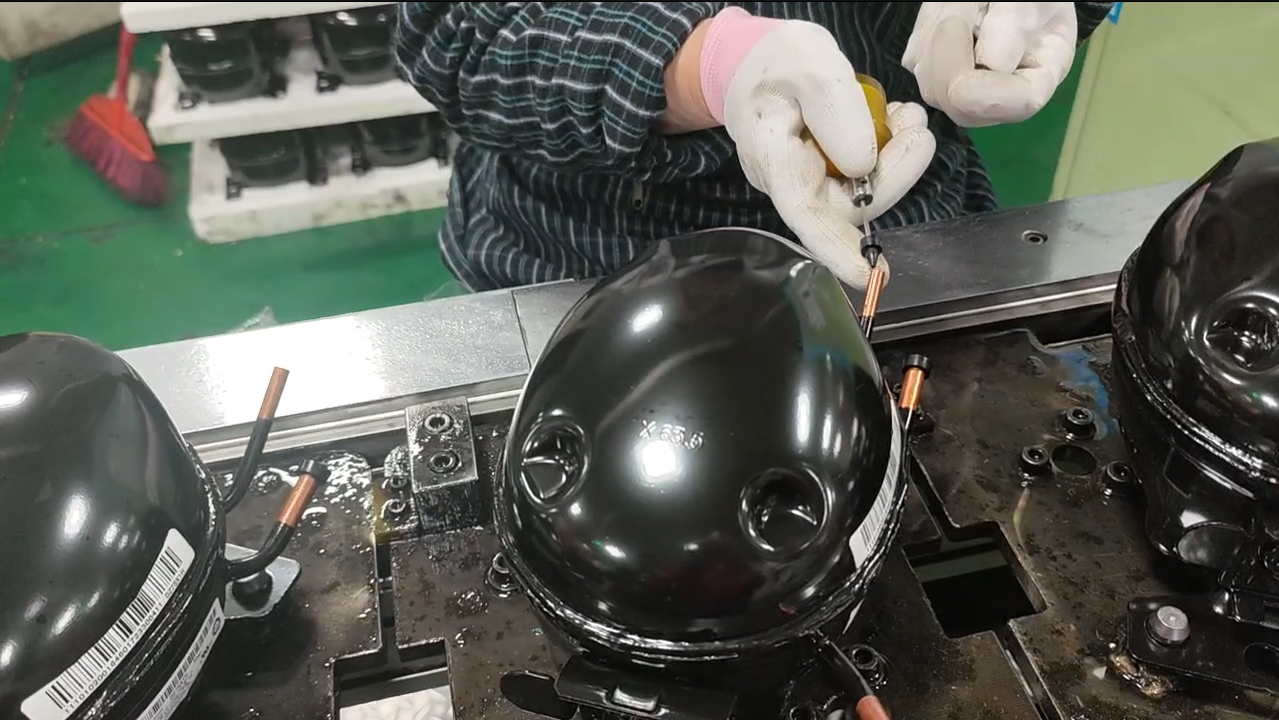
排气管内孔与矫管针配合精度达0.025mm,同时来料压缩机排气管空间角度一致性偏差很大(±5°),且前道折弯及焊接工序也会导致累计误差。客户现阶段完全采用人工完成此工序,而传统工业机器人在配备超高精度3D视觉的情况下,仍然无法满足良率需求。
方案构成
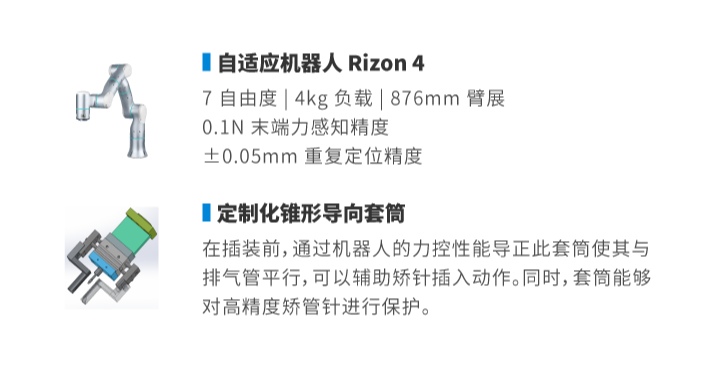
项目优势
新颖工装 辅助柔顺插入
该方案采用自适应机器人配合锥形导向套筒,在对高精度矫管针进行保护的同时,可以通过机器人的力控性能柔顺导正套筒,使其与排气管平行,从而辅助矫管针插入动作。
高误差容忍 防止工件损坏
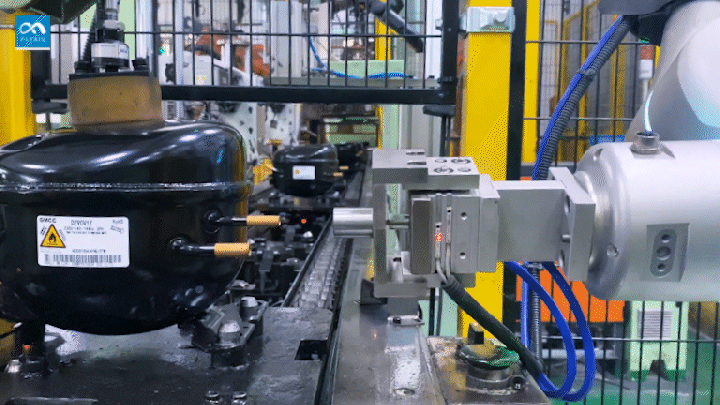
自适应机器人工业级力控能力可兼容压缩机排气管的位置误差、空间角度误差、折弯累计误差,满足高达0.025mm配合精度,保证矫管针准确、到位地插入无问题排气管,避免出现意外折针等情况。
力反馈判断 助力智能管理
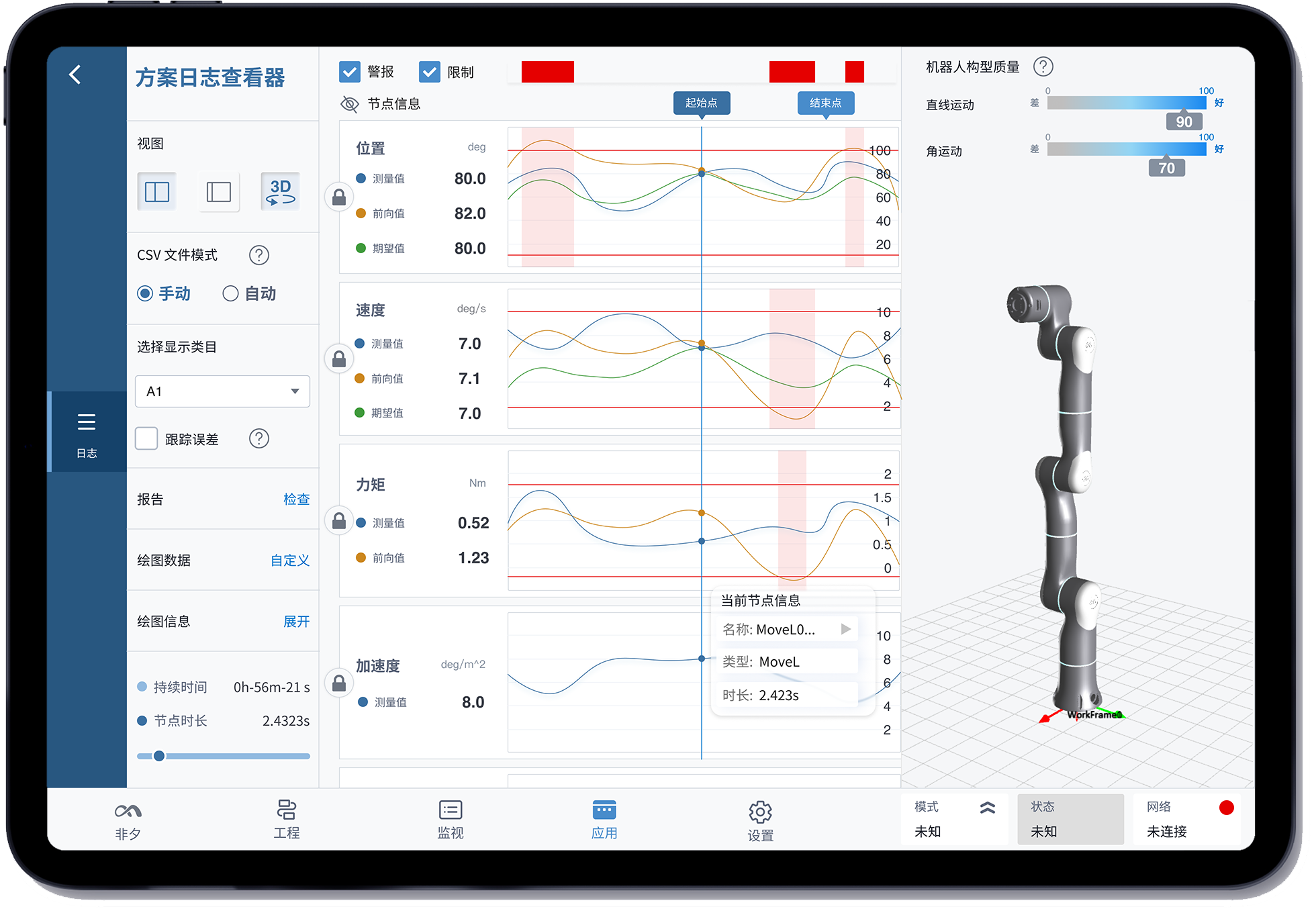
通过高达0.03N的末端力觉反馈,该方案可以灵敏判断排气管检测结果,并进行实时报告;依据具体需求,还可以实时显示力觉曲线以辅助判断或产线智能管理。
高效通用 实现降本增效
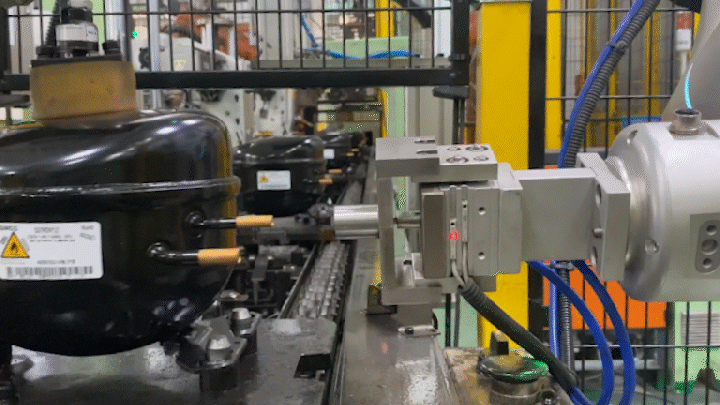
该方案实际运行中检测节拍≤3s,工位节拍≤5.5s(含输送时间);无需视觉和其他专机设备,使整体方案具有高性价比。以自适应机器人配合锥形导向套筒为主的方案可以兼容多种管径产品,符合客户小批量、多品种的生产需求。